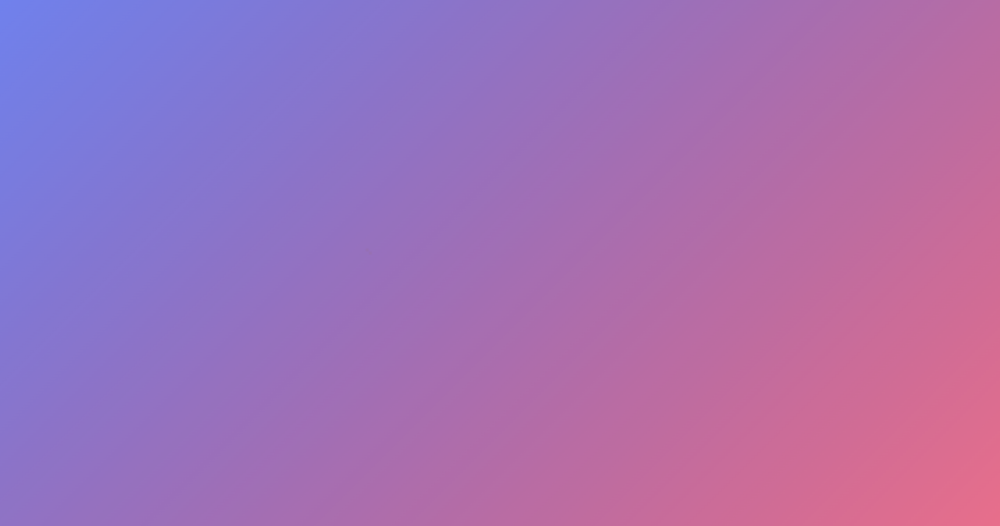
13
四月Supply Chain Optimization
Lean principles have revolutionized the way businesses approach supply chains, focusing on eliminating waste, simplifying processes, and maximizing value for customers.
The concept of lean originated in the auto manufacturing industry, where it was pioneered by the Toyota Production System in the 1950s. As a result, many industries have incorporated lean principles into their operations. We will delve into the practical applications of lean principles in optimizing supply chains, improving operational efficiency, and promoting a culture of continuous improvement.
Understanding Lean Principles in Supply Chains
---------------------------------------------------------
Lean principles emphasize minimizing waste and maximizing value by streamlining processes, improving productivity, and reducing costs without compromising quality. Some key lean concepts are:
1. Flow: This refers to the continuous and smooth movement of products through the supply chain. Pull refers to production and ordering in line with actual customer needs. Continuous improvement involves incremental changes driven by engaged employees and empowered teams. 4. Just-in-Time (JIT): Producing or ordering products just when they are needed to minimize storage and reduce inventory costs. Mapping streamlines processes and eliminates process optimization an waste reduction.
Benefits of Applying Lean Principles to Supply Chain Management
---------------------------------------------------------
Lean principles provide numerous benefits in supply chain management:
Lean principles reduce costs by minimizing waste. Implementing lean principles improves product quality through standardized processes. JIT and flow management enable faster responses to changing market conditions. Lean principles provide transparency into supply chain activities. Innovation and improvement characterize lean culture.
Implementing Lean Principles in Your Supply Chain
------------------------------------------------
Effective implementation of lean principles demands dedication and commitment. Lean implementation involves the following key steps:
Establish a lean implementation team to lead the transformation and provide guidance. Identify waste through lean methods and analysis. Empowered employees drive lean transformation. 4. Implement just-in-time and flow-based production strategies and standardized productivity measures. 5. Implement metrics for measurement, documentation, and evaluation and maintain continuous improvement and continuous improvement.
Best Practices for Adopting Lean in Supply Chains
-------------------------------------------------
When adopting lean principles in supply chain management, keep the following points in mind:
1. Plan your transition from traditional production methods to lean-based ways to ensure smooth order fulfillment and prevent shipping problems, stock backlog, or communication failures between dispatching teams and customers. Stakeholders must be engaged and informed. 3. Leverage existing technology to automate supply chain management processes improve productivity through consistent and reliable analytics and efficiency within and collaboration, value stream mapping, streamlining processes or business continuity planning. Invest in data analytics for improved efficiency. Ensure efficient product flow through supply chain analysis and monitoring.
Reviews